De voorbije dagen gaven we je updates (
1,
2,
3) vanaf de beursvloer van EuroBike 2023. Het zwaartepunt lag bij e-bikes en bij mobiliteit in brede zin. Maar naast grote stands van e-bike-fabrikanten en toeleveranciers van e-bike-technologie, waren er dit jaar opvallend veel kleine spelers die lieten zien wat ze met een printer kunnen. Een 3D-printer, meer bepaald.
Tekst: Jeroen van den Brand // Foto’s: Arjan Kruik & Jeroen van den Brand
3D-printen niet langer alleen voor prototypen
Tijdens eerdere edities van de EuroBike zagen we 3D-geprinte onderdelen. 3D-printen is dan ook niet echt nieuw meer. Al heel wat jaren maakt de technologie langzaam een opmars. In eerste instantie ging dat veelal over kunststof onderdelen, waarbij de printtechnologie het mogelijk maakte om snel visuele en zelfs functionele prototypen te maken. Het printen van metalen is stilaan ook gemeengoed. Niet alleen voor functionele prototypen, maar ook voor productiewerk. 3D-printen biedt namelijk veel meer vormvrijheid. Je hoeft als ontwerper je niet meer af te vragen of een onderdeel nog wel op een frees- of draaibank te maken is. Bovendien bespaart het materiaal; je smelt (met een laser) alleen materiaal samen dat je werkelijk gebruikt.
3D-printen is echter nog steeds een relatief tijdrovende methode. Om die reden is de inzet van printtechnieken bij grote productiepartijen nog steeds beperkt. En op EuroBike 2023 zagen we dan ook vooral de kleinere spelers hun printkunsten tonen. Sommigen produceren relatief eenvoudige producten, anderen omarmen volop de vormvrijheid die je met 3D-printtechnieken hebt. En, zoals je hier onder zult zien, dat gaat niet alleen over kleine onderdelen. Ook frames rollen tegenwoordig uit de printer…
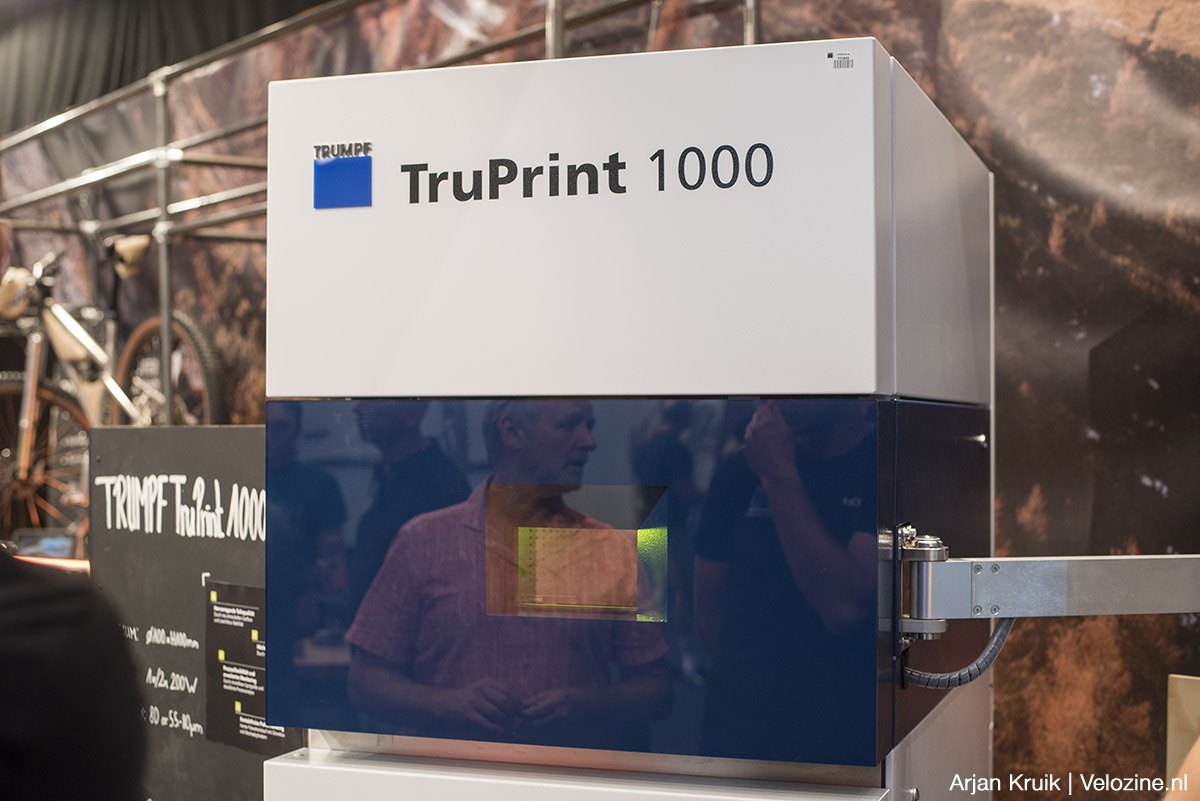
Op de stand van Trickstuff stond de firma
Trumpf (Nee, niet die van ‘We’re gonna print that wall….!’), fabrikant van 3D-printers.
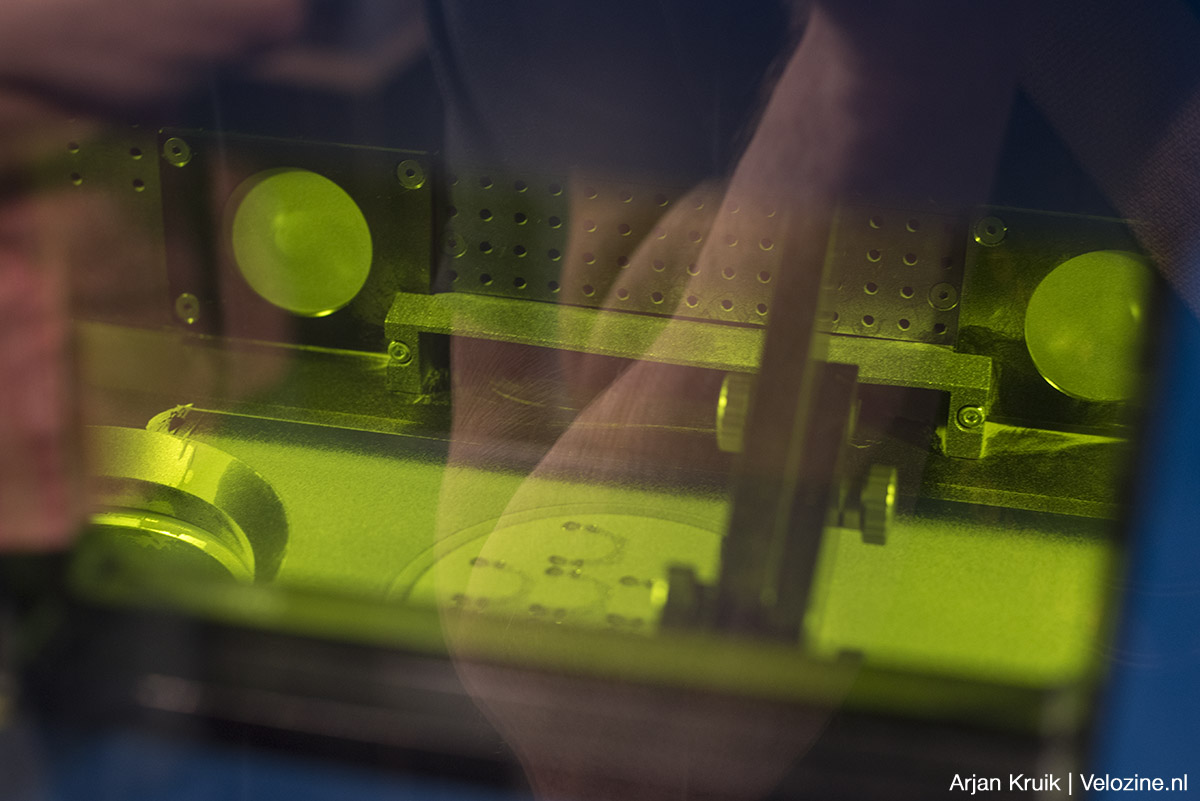
En bij alleen het laten zien van de machine bleef het niet. Er werd volop geprint. Deze specifieke printer werkt volgens het poeder-laser-principe, meer specifiek: “Selective Laser Melting” (SLM). Bij SLM smelt een laser metaalpoeder aan elkaar. Telkens een dun laagje, waarna de puck waarop de producten worden geprint, iets naar beneden zakt. Hierna voegt de machine met een schraper een nieuwe laag poeder boven op de print toe, waarna de laser een nieuwe laag metaal aan de producten print.
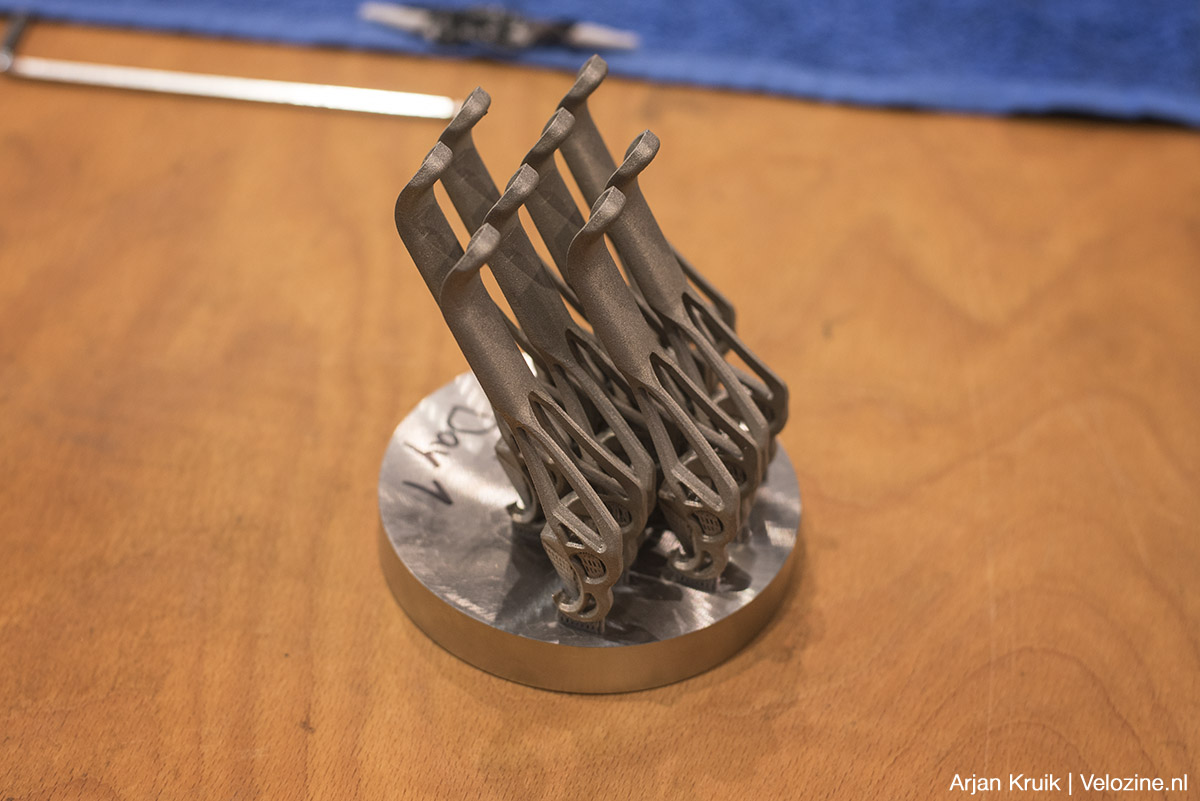
Hier zie je zo’n puck met daarop acht titanium remhendels. Na het printen worden ze handmatig verwijderd van de puck en verder nabewerkt.
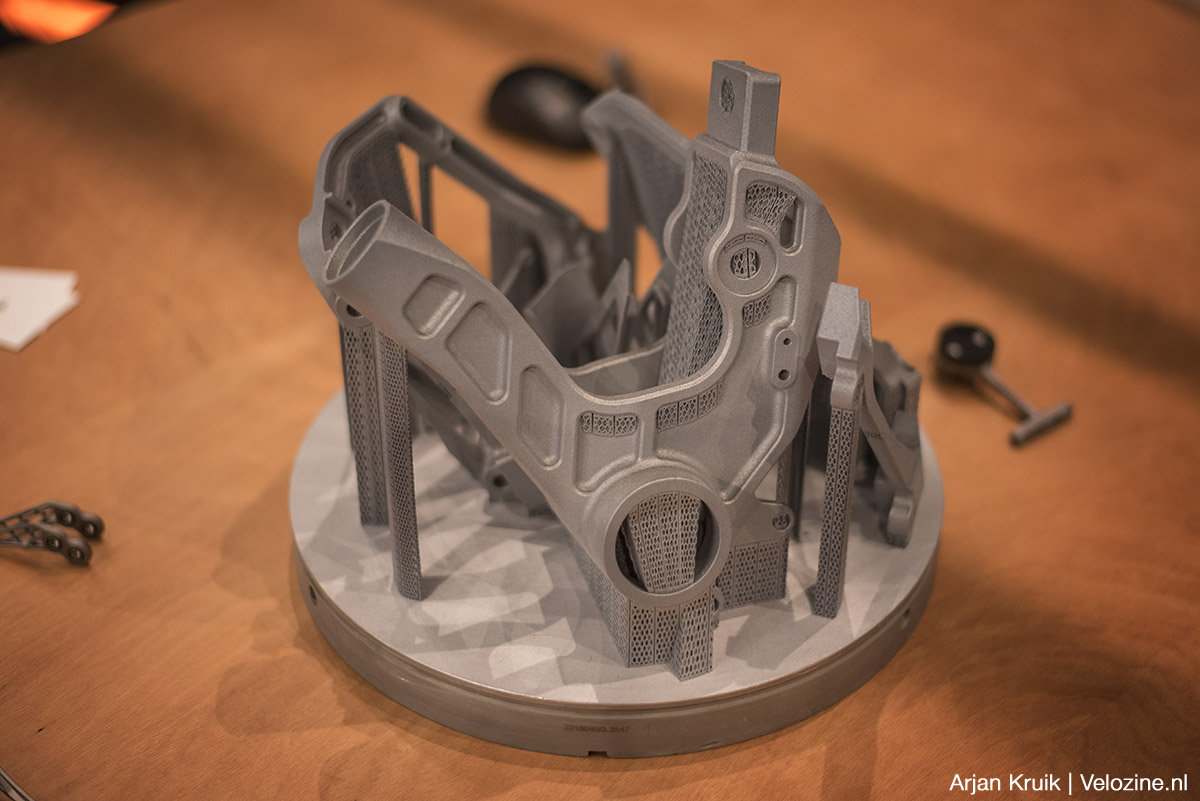
Om een product zo gunstig mogelijk te printen zijn er vaak ondersteuningsconstructies nodig. In bovenstaand voorbeeld zie je allerlei rastervormige ondersteuningen. Die garanderen de vorm- en plaatsnauwkeurigheid tijdens het printen. Na het printen worden deze hulpconstructies verwijderd.
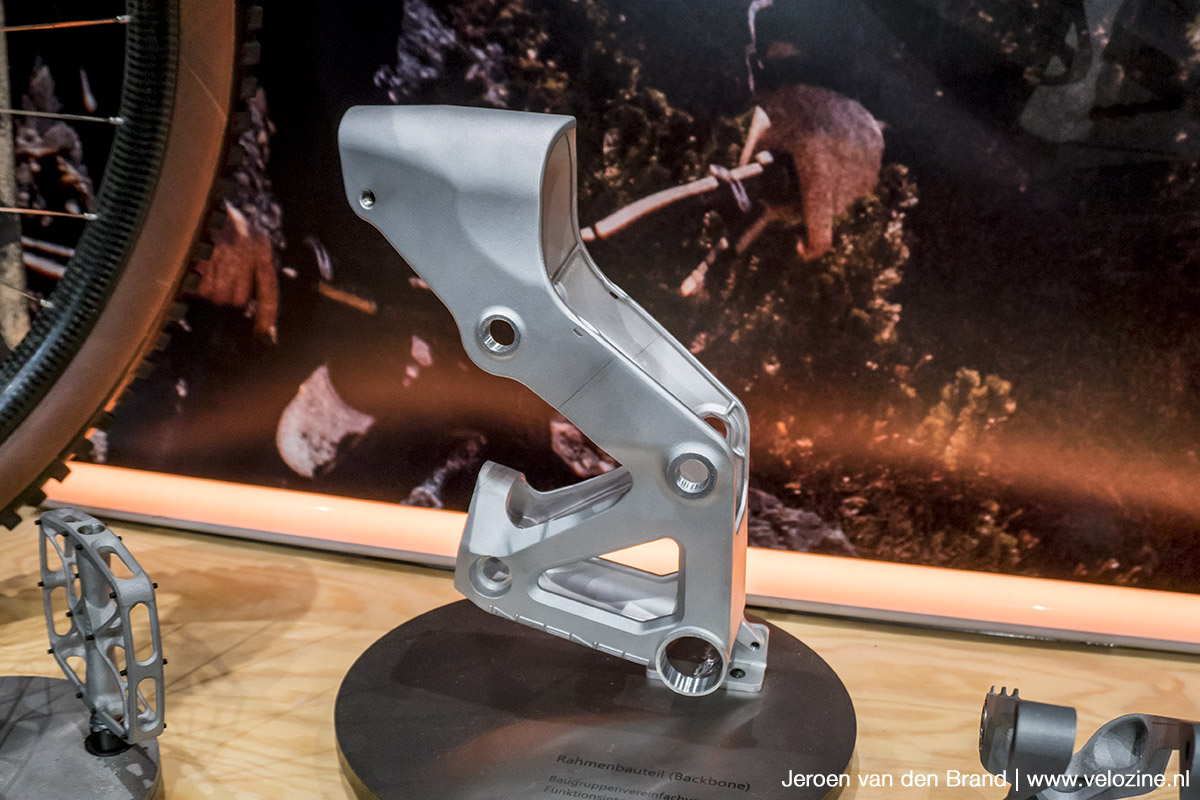
En hoewel nauwe toleranties steeds beter mogelijk zijn, is machinale nabewerking van bijvoorbeeld lagerpassingen nog wel nodig. Ready-to-go-printen is dus in de regel niet het geval. Hierboven zie je overigens een vrij fors aluminium framedeel dat Intense in de
proto’s van z’n nieuwe downhillbike gebruikte.
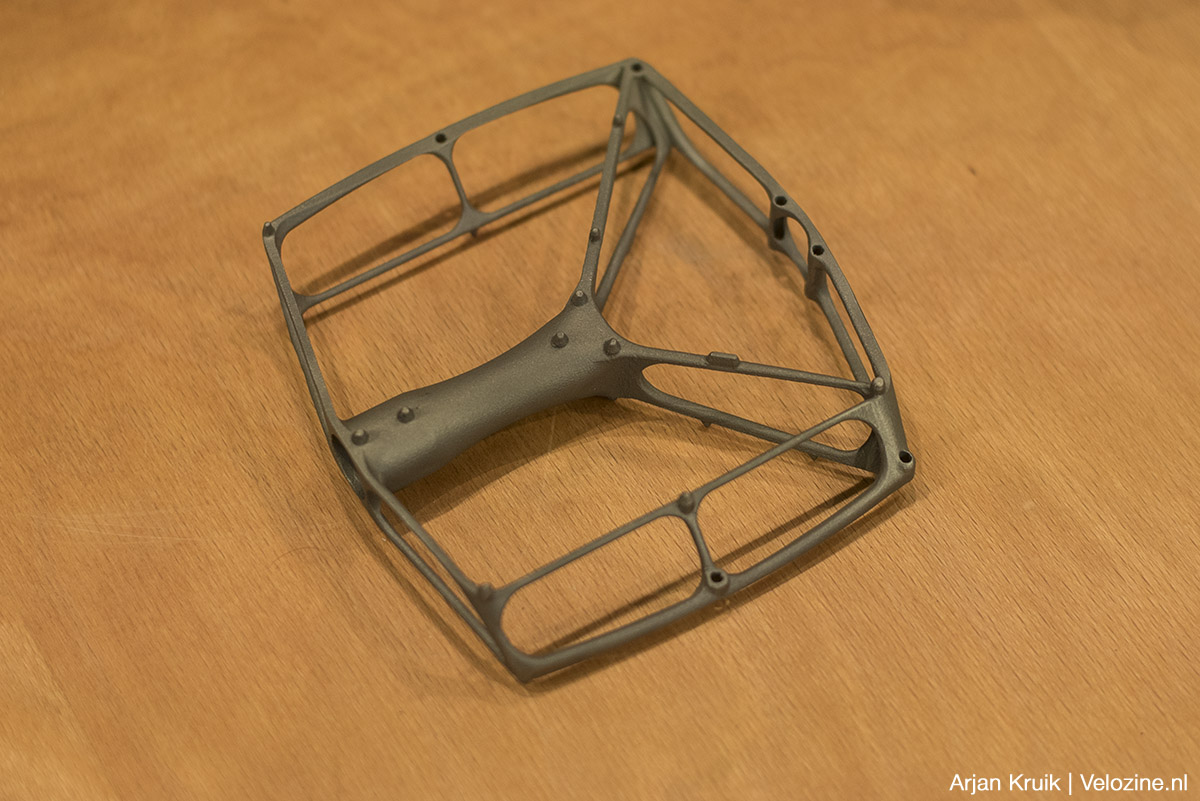
Printen maakt het mogelijk om vormvrijer te zijn. Dunne, gekromde vormen zoals bij dit titanium pedaal zijn niet gemakkelijk op een freesmachine te maken.
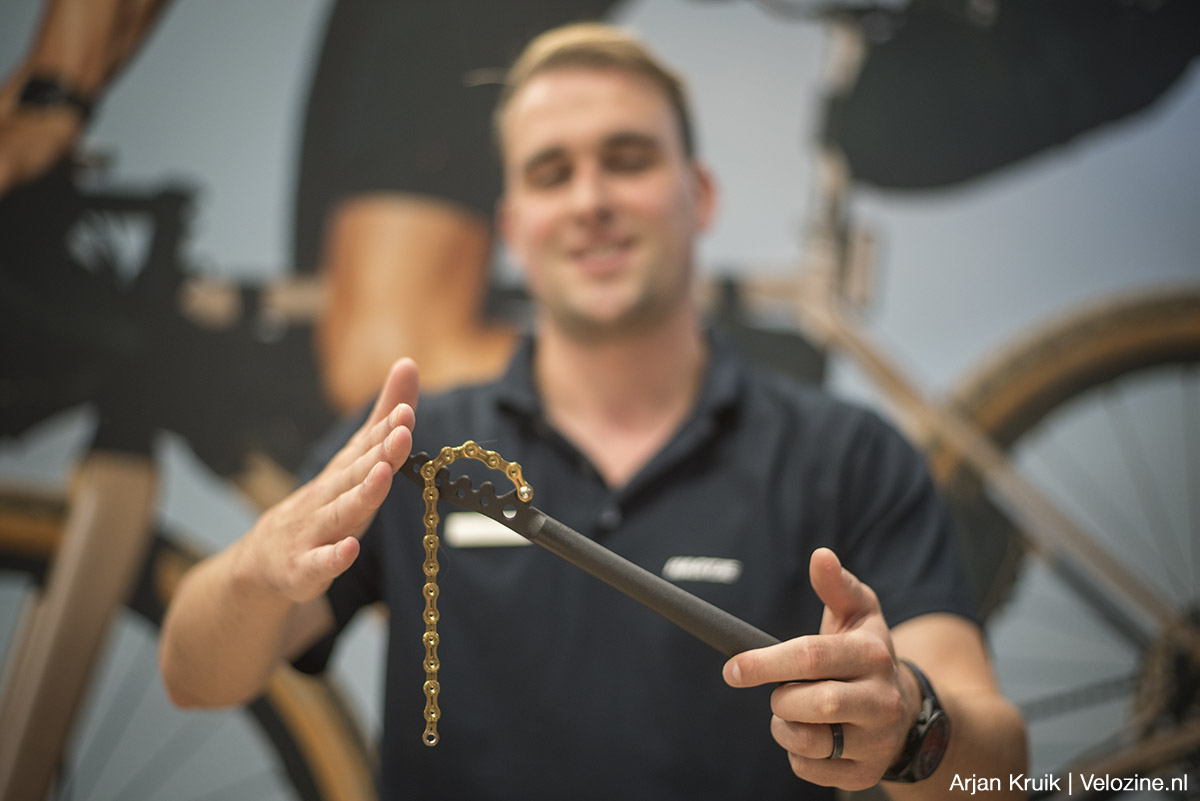
Silca ken je van
exclusieve, sjieke onderdelen. Ze zijn óók fan van printen. Zij gebruiken de 3D-printtechniek om een superlichte kettingzweep van van titanium te maken. Silca maakt hierbij niet extreem gebruik van de vormvrijheid die de printtechniek biedt. Dit is meer een gevalletje ‘gewoon, omdat het kan’.
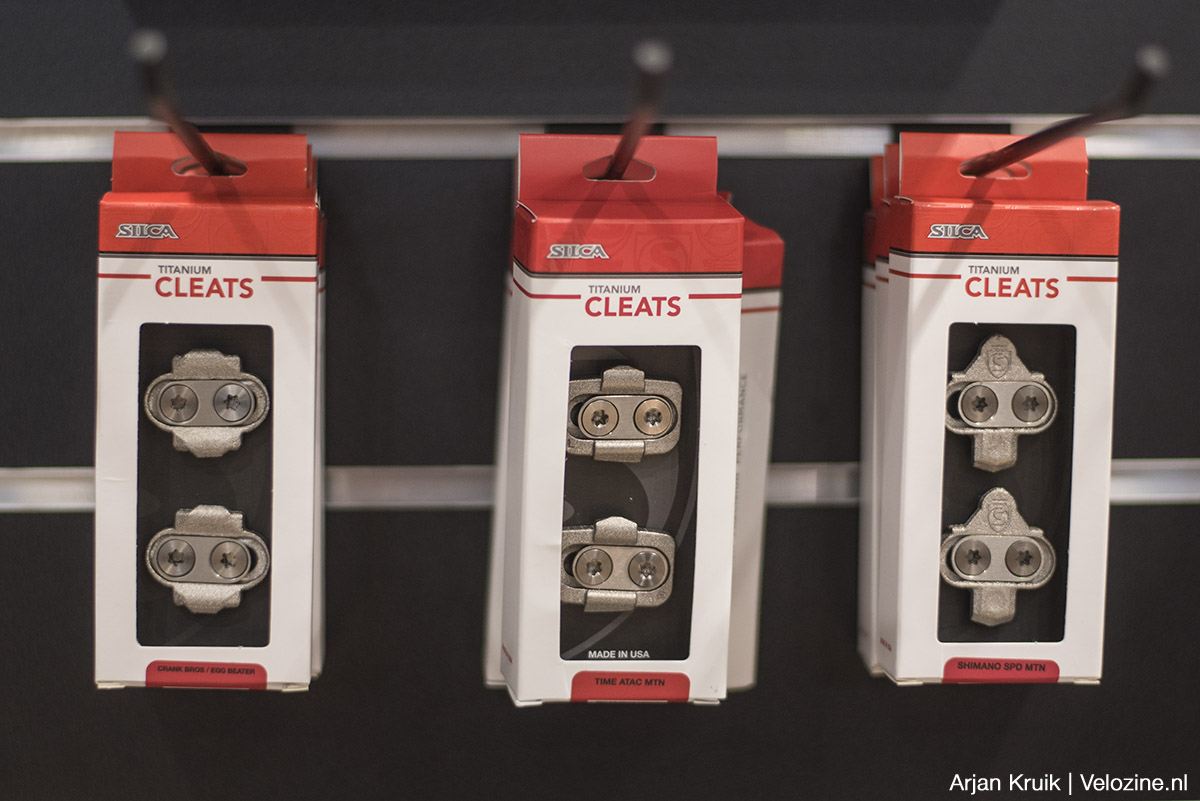
Oók deze pedaalplaatjes zijn van titanium. Ze zijn lichter dan de stalen equivalenten – zover je dat belangrijk vindt. In het geval van de Time-plaatjes (midden) zijn ze ten opzichte van het messing dat Time gebruikt, ook een stuk slijtvaster. Schoenplaatjes hebben diverse schuine hoeken en curves die lastig te frezen zijn. Het merendeel wordt dus gesmeed. Voor smeden heb je echter (dure) matrijzen nodig. 3D-printen is dan best een interessante optie, zeker wanneer je relatief kleine oplages maakt.
Framedelen en zelfs complete frames worden geprint
Hierboven zag je al enkele voorbeelden van framedelen die in metalen worden geprint. Steeds meer kleine framebouwers passen 3D-printtechnieken toe om een uniek ontwerp neer te zetten waar fraaie looks én technisch vernuft bij elkaar komen.
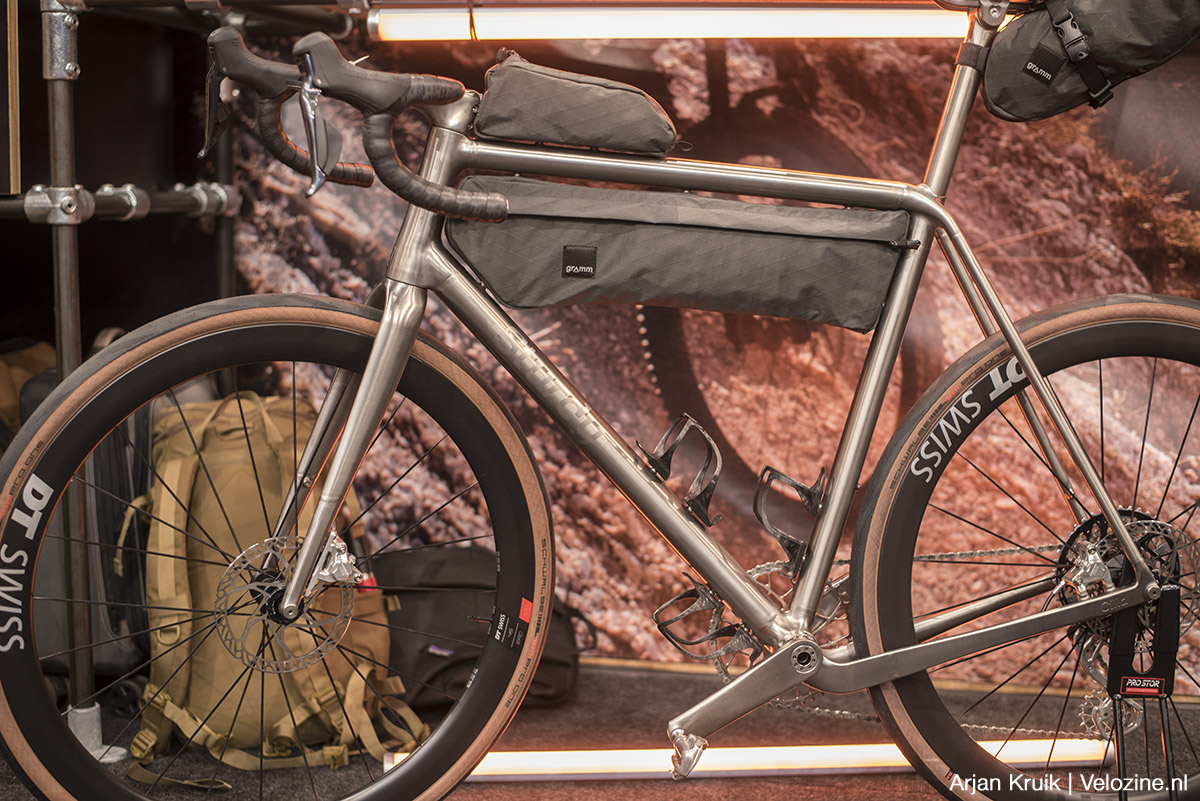
Tom Sturdy uit Engeland bouwt z’n titanium-creaties met behulp van 3D-printen.
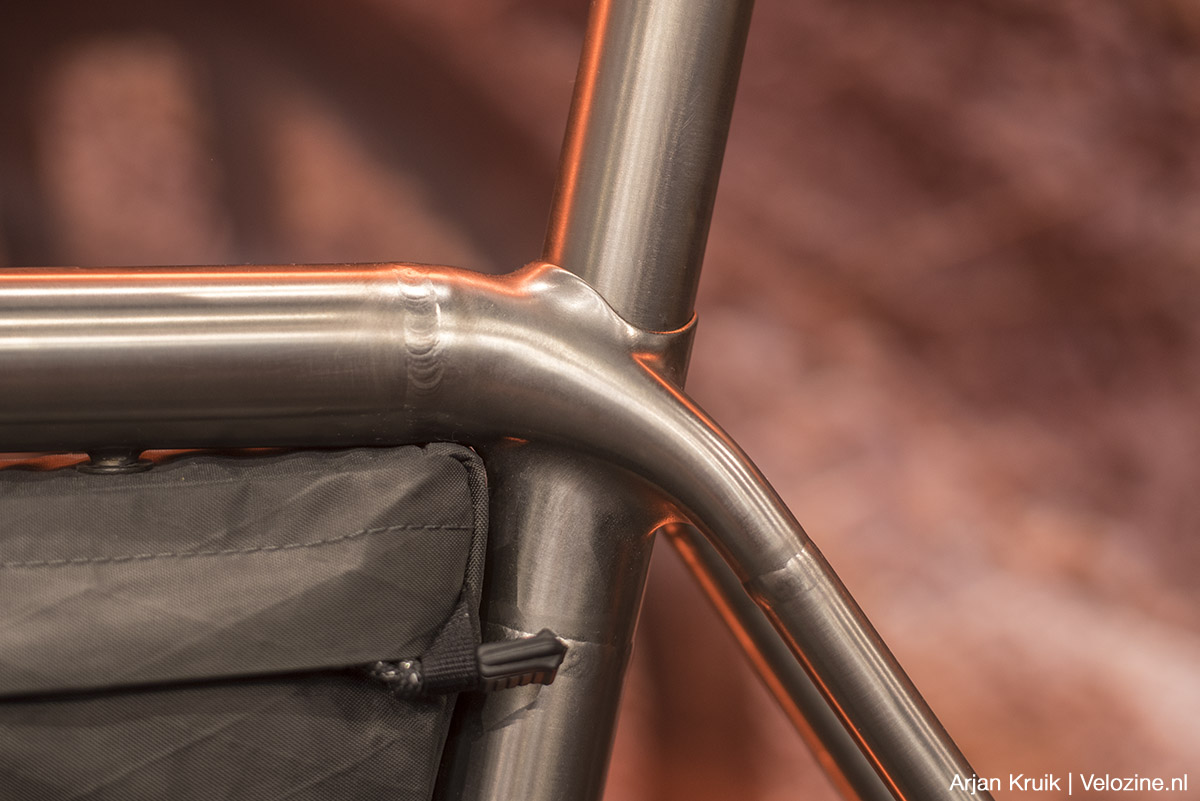
Framedelen zoals de koppeling tussen bovenbuis, staande achtervork en zitbuis zijn geprint.
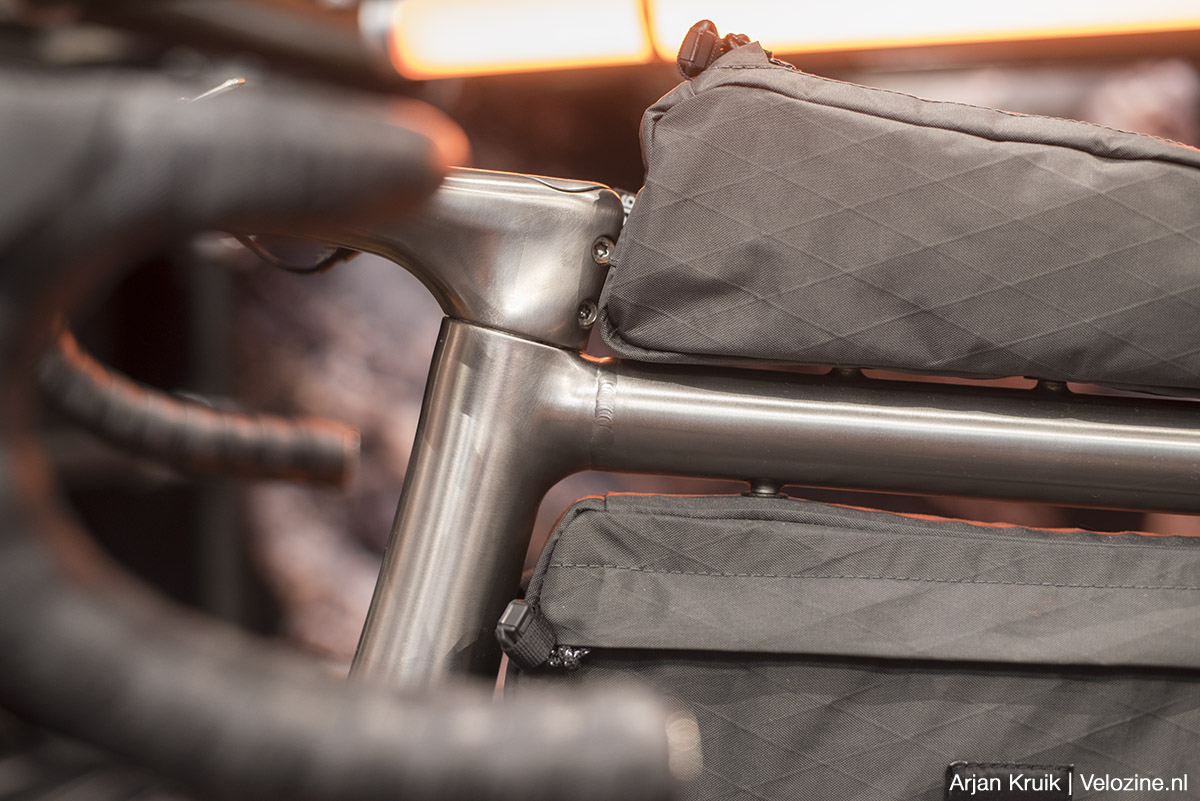
En niet alleen de balhoofdbuis, óók de volledige cockpit (stuurpen én stuur) komen uit de printer.
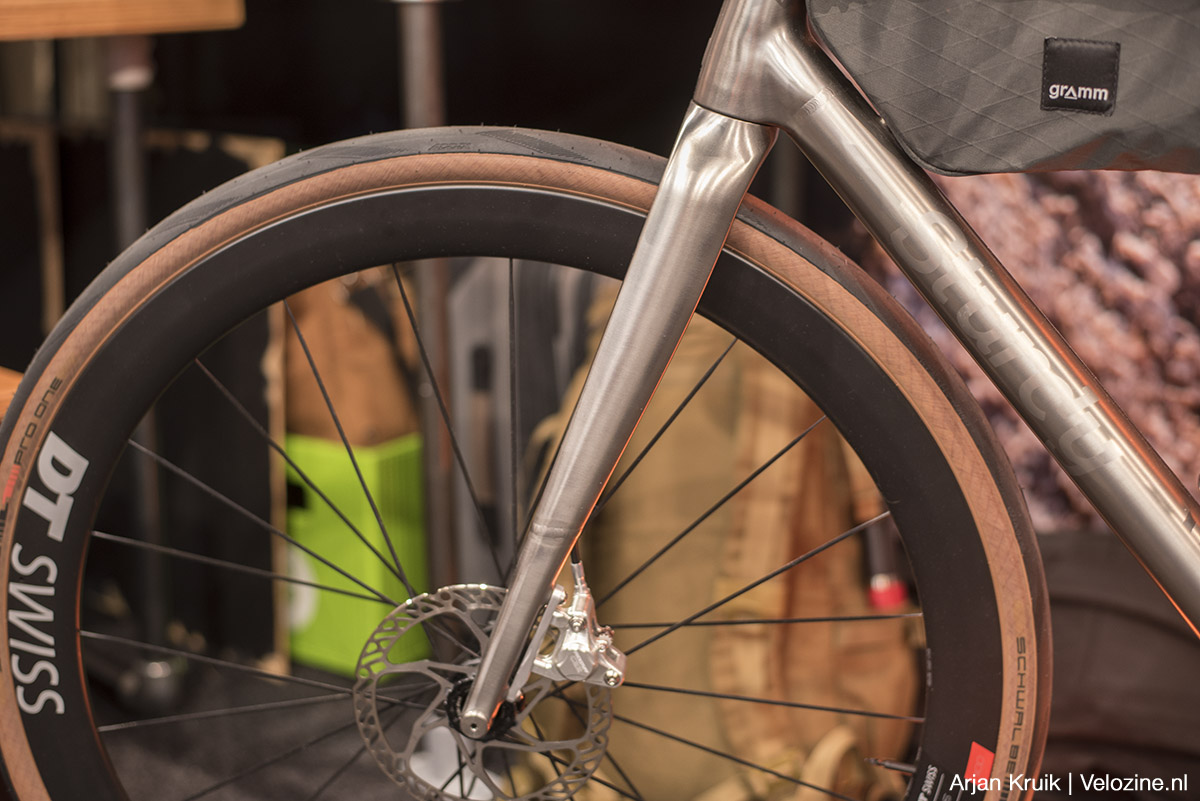
Titanium is relatief sterk, licht en trillingsdempend. Ideale eigenschappen voor een voorvork. Inmiddels zijn printtechnieken dermate ver gevorderd dat het zwaarst belaste onderdeel van een fiets – de voorvork – dus óók gewoon geprint kan worden. Tom Sturdy gebruikt de techniek om zo 100% op de klant afgestemde geometrie te kunnen aanbieden.

Oók
Huhn Cycles combineert geprinte onderdelen samen met standaard buizen om frames in staal en titanium te bouwen.
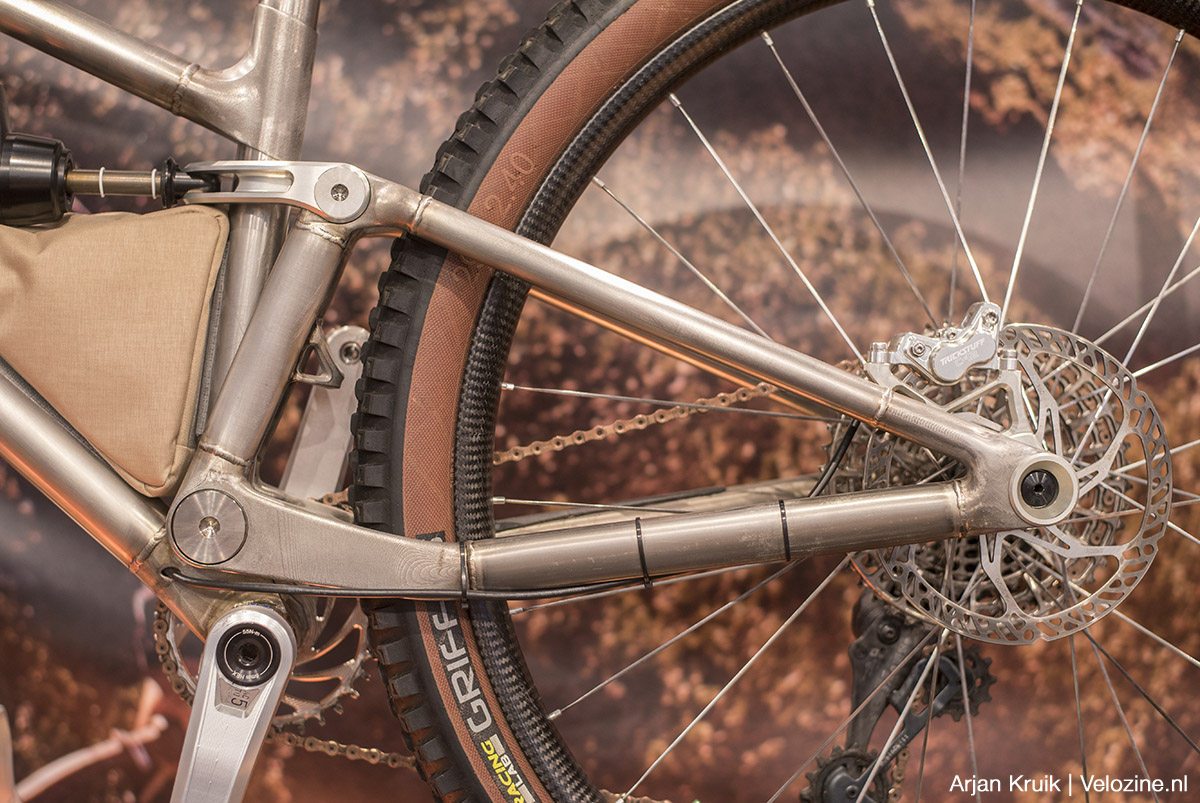
Alle koppelstukken tussen de buizen zijn 3D-geprint.
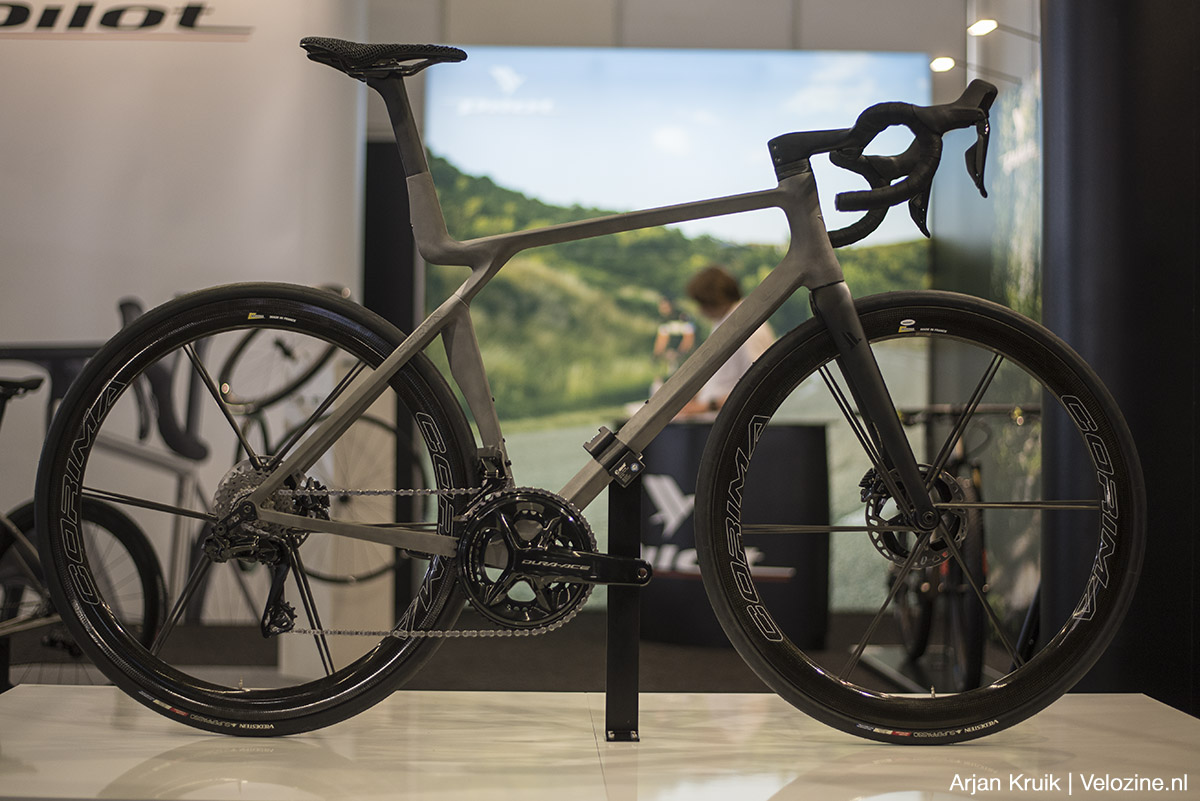
Ook het Nederlandse
Pilot Cycles experimenteert al enige tijd met het 3D-printen van titanium.
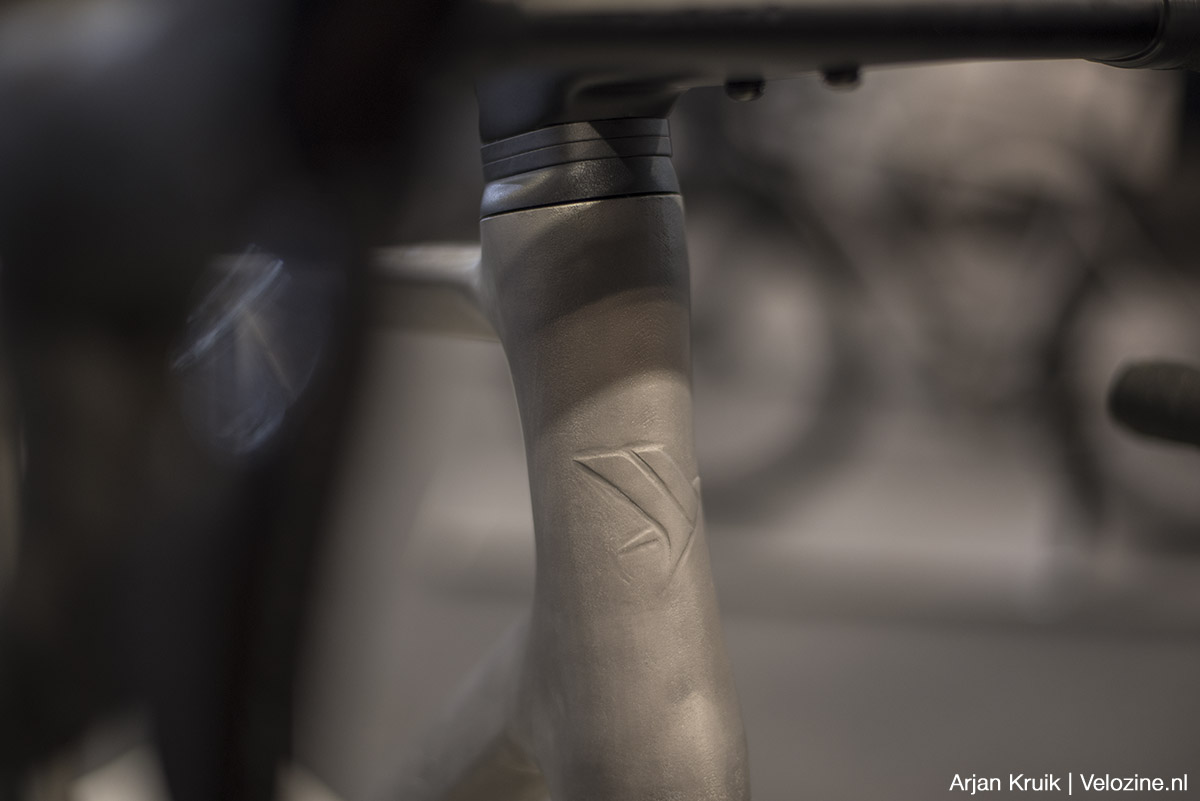
De Seiren die ze op EuroBike 2023 toonde is nog steeds een prototype, maar het bedrijf werkt hard naar een versie die ook daadwerkelijk in productie gaat komen.
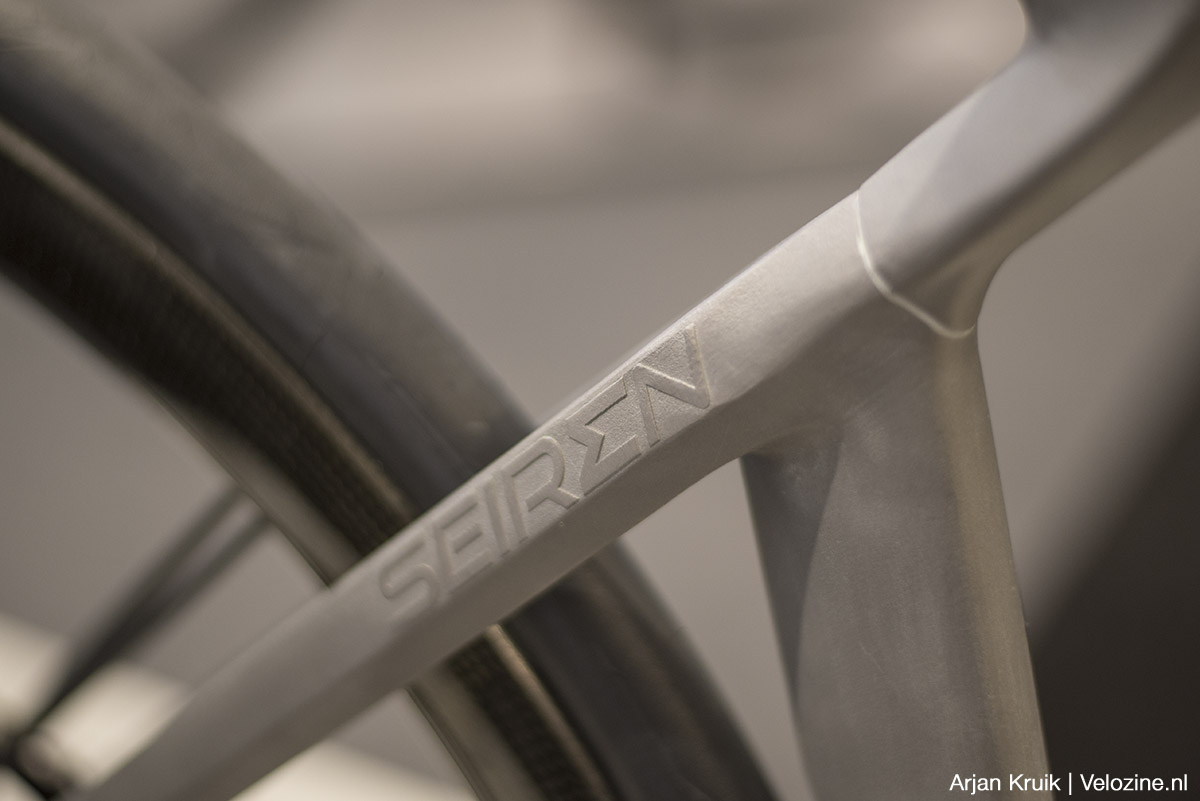
In tegenstelling tot Sturdy en Huhn die je hier boven al zag, past Pilot nergens een standaard buis toe. Alle framedelen zijn geprint. Ja, het gaat hier dus nog steeds over losse framedelen, simpelweg omdat de printer niet groot genoeg is. Pilot lijmt vervolgens drie framedelen samen tot één frame.
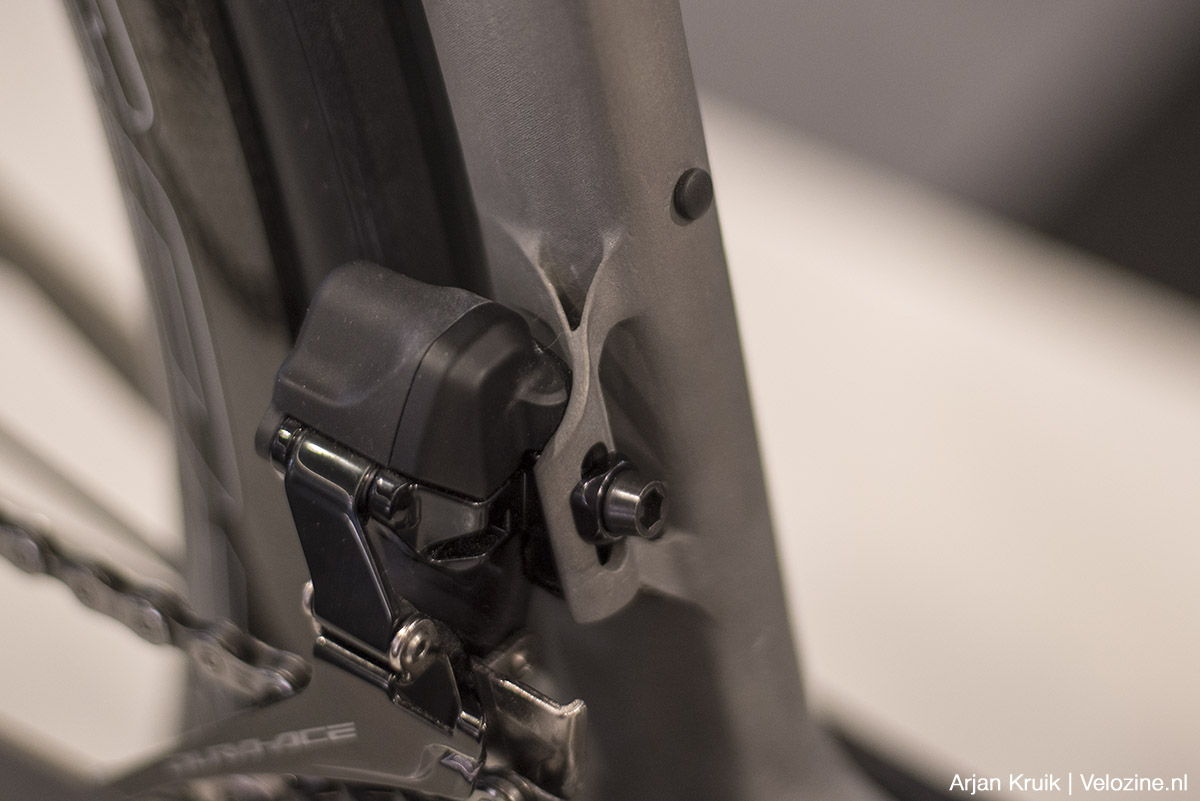
“U wilt een voorderailleur monteren? Printen we de montagebeugel gewoon voor u mee!”
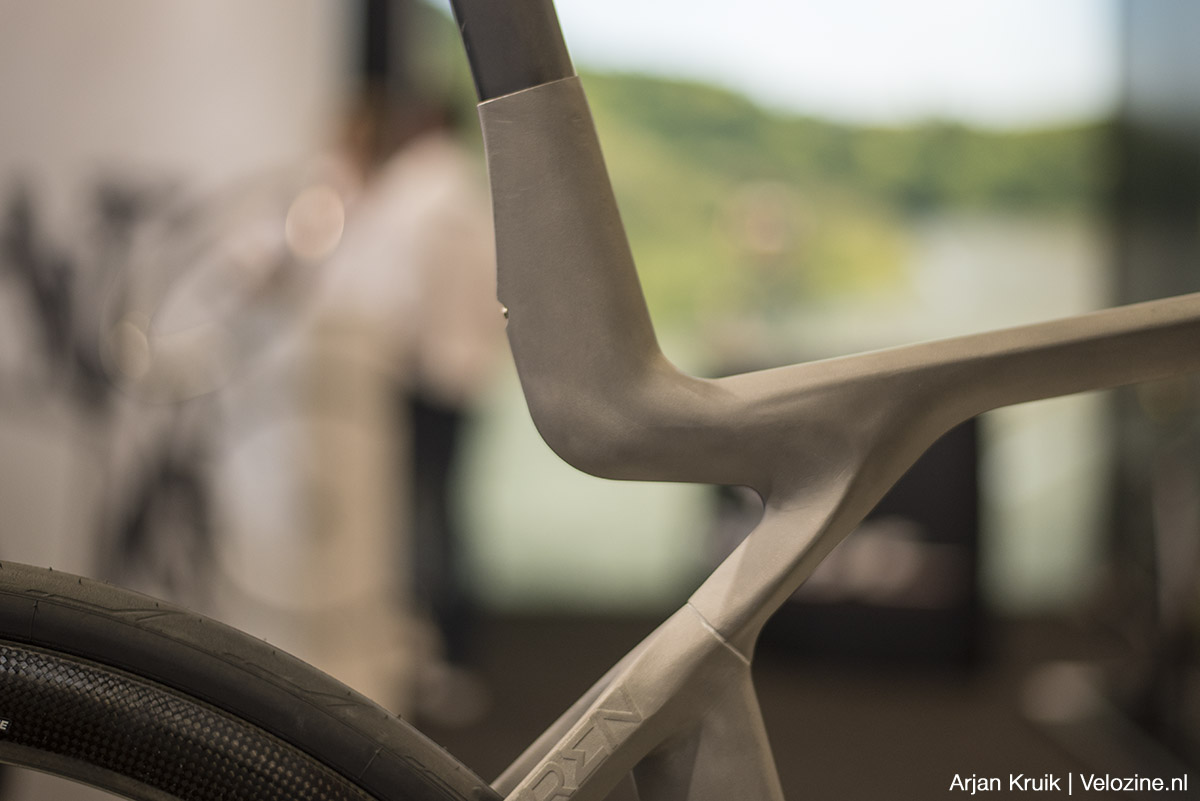
De vormvrijheid van 3D-printen maakt dat vormen niet strikt de norm hoeven te volgen.
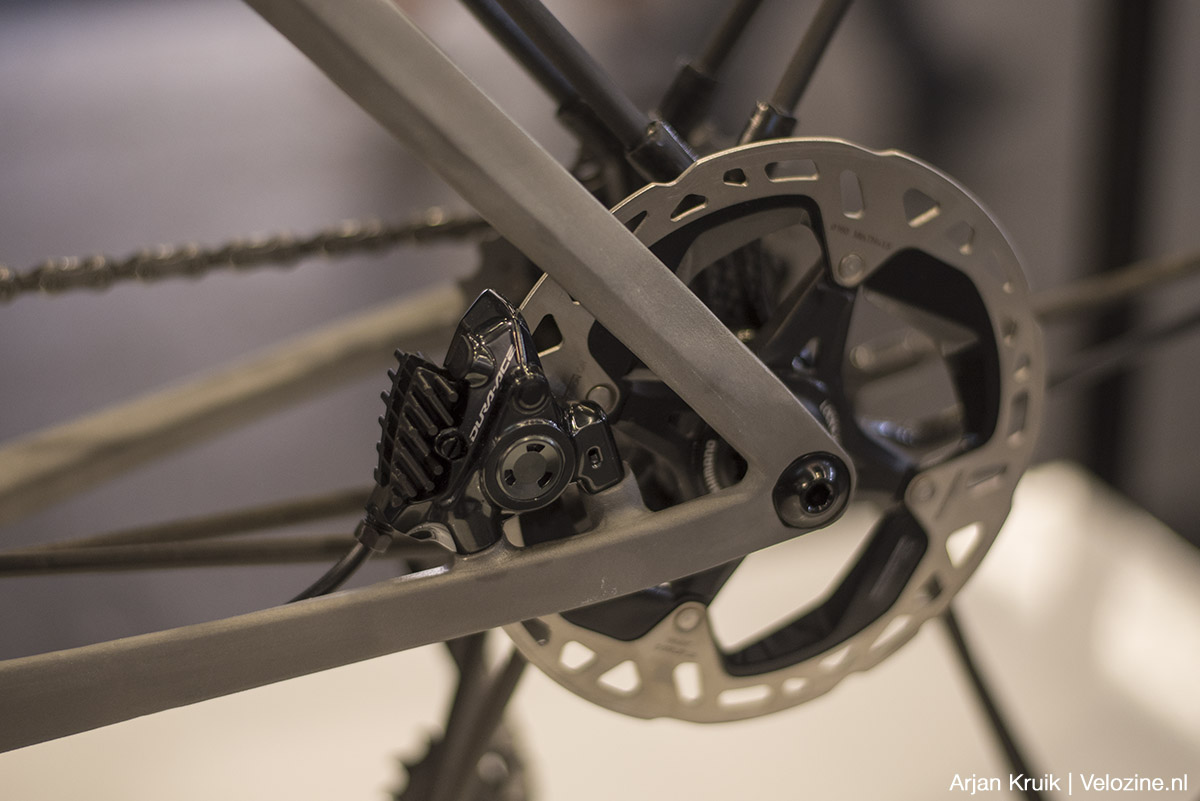
Al is er natuurlijk niets mis met strak en simpel.
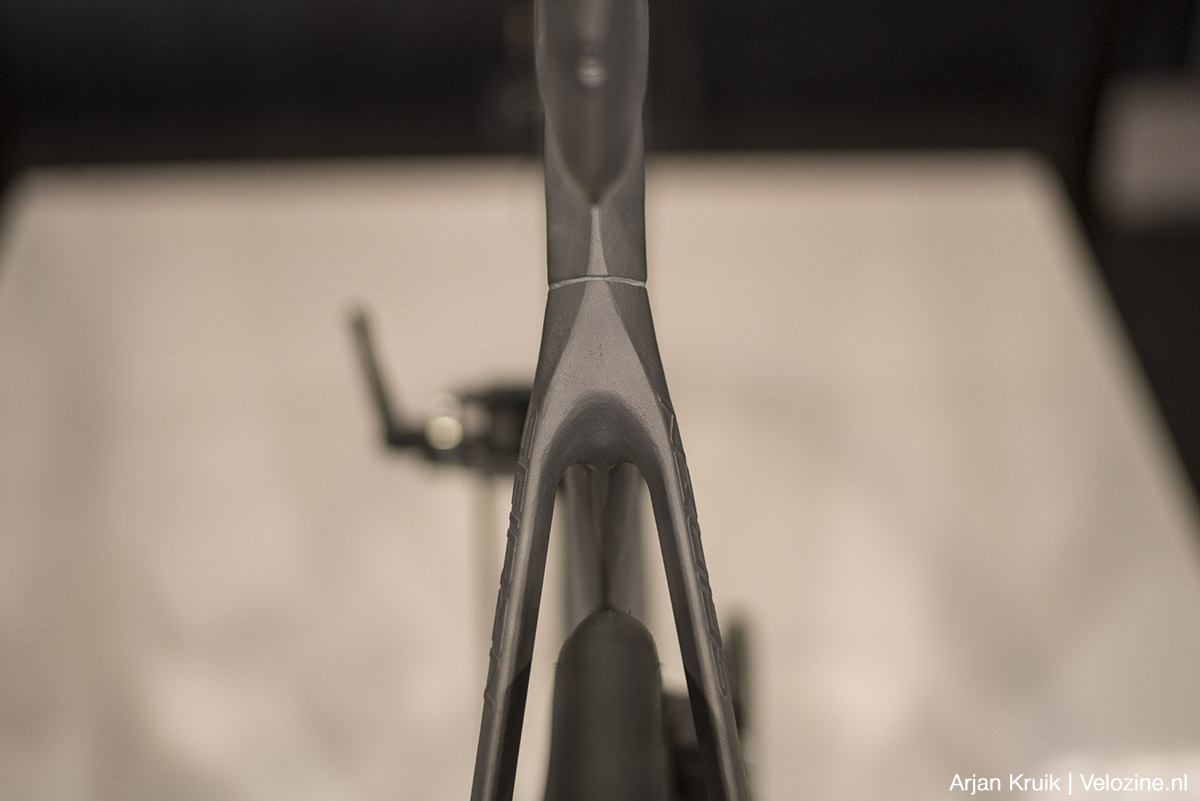
De lijmnaden zijn bij het prototype dat we op EuroBike 2023 zagen nog wel duidelijk zichtbaar.
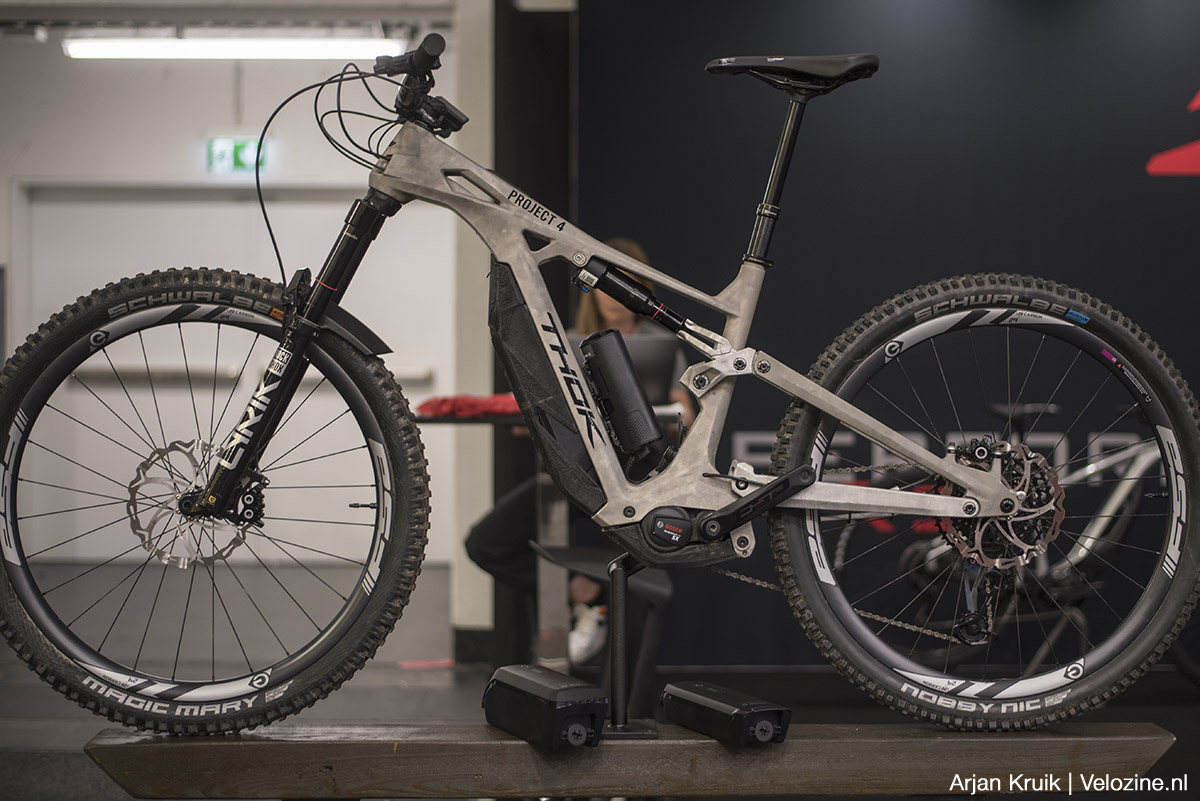
Het Italiaanse Thok toonde hun Project 4. Een e-mountainbike met een aluminium frame dat eveneens is geprint. Ook zij liepen tegen de fysieke beperkingen aan van printers. We hebben de lasnaden niet gevonden, maar ook het voorframe is uit meerdere printdelen samengelast.
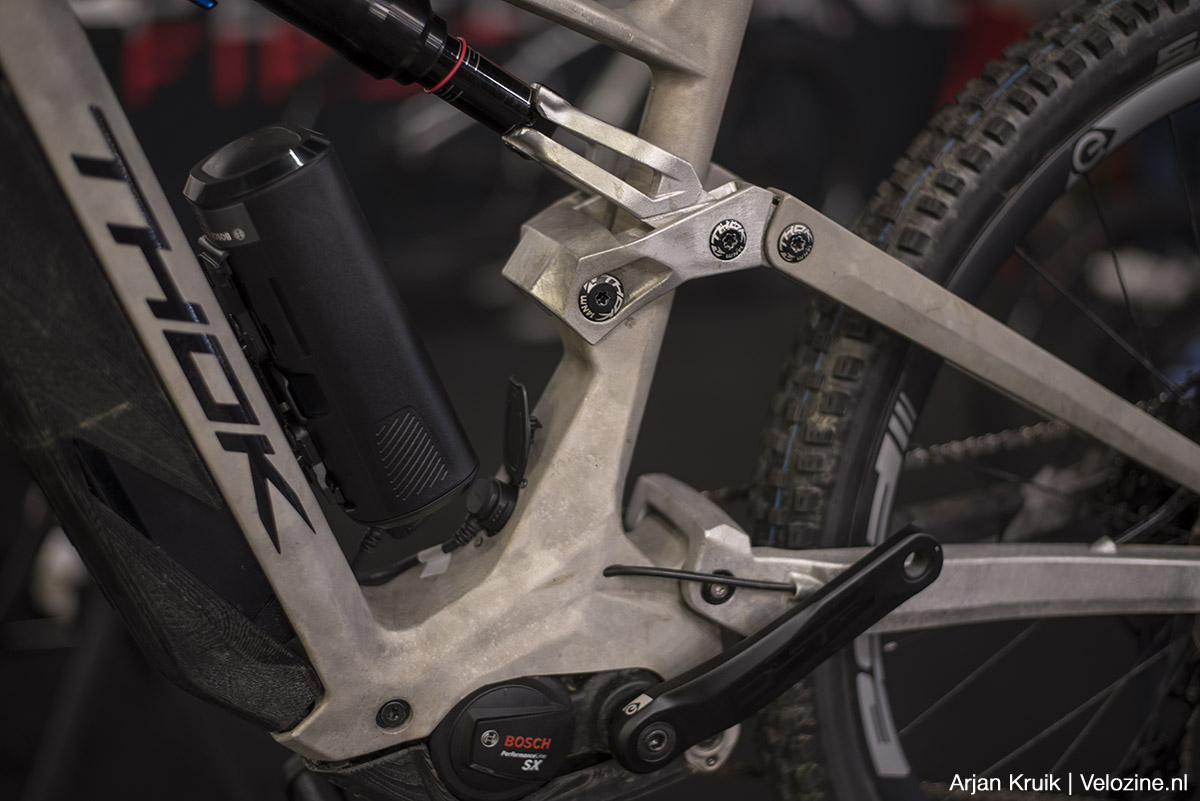
Thok gebruikt de 3D-printtechniek om in aluminium snel een functioneel prototype te maken. Uiteindelijk vertaalt Thok dit ontwerp naar een carbon-versie.
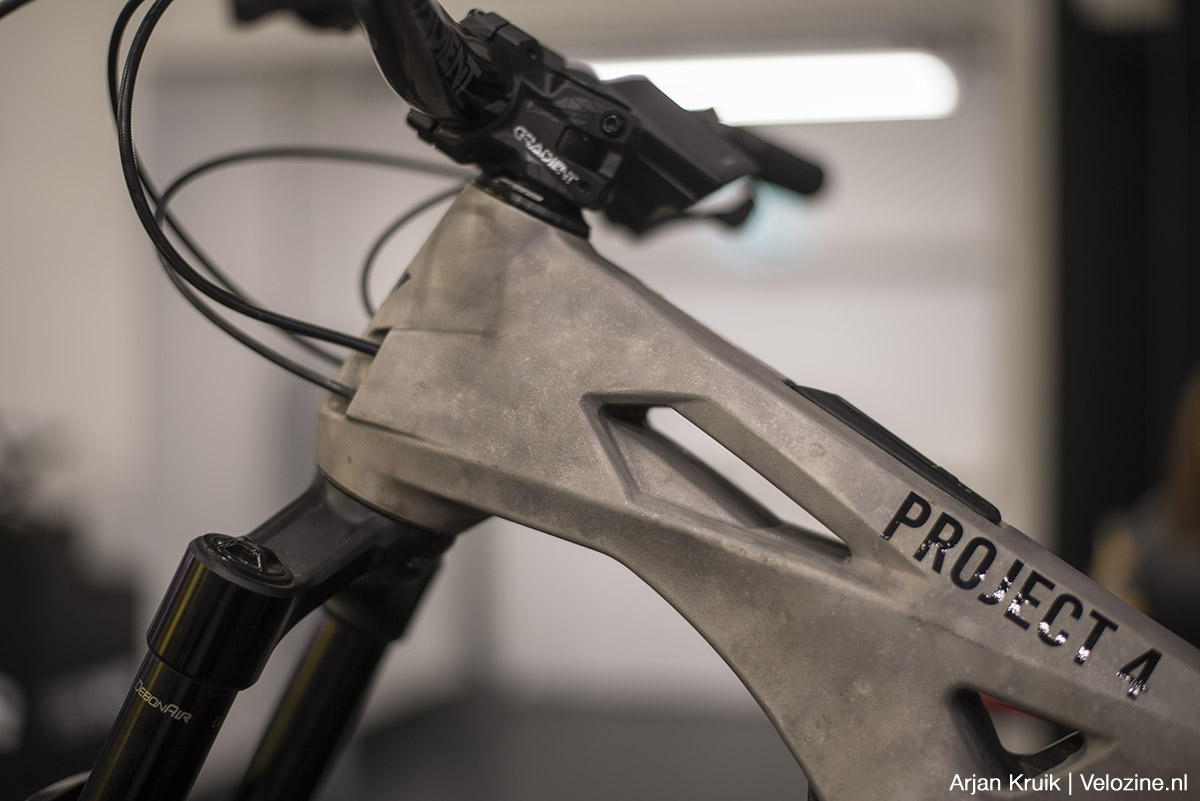
Over de looks van het frame van niet te twisten, maar het rauwe aluminium vinden we wel passend bij het hoge Terminator-gehalte van het ontwerp.